Source: 2011 Q3 Beartracks, Pat Fagan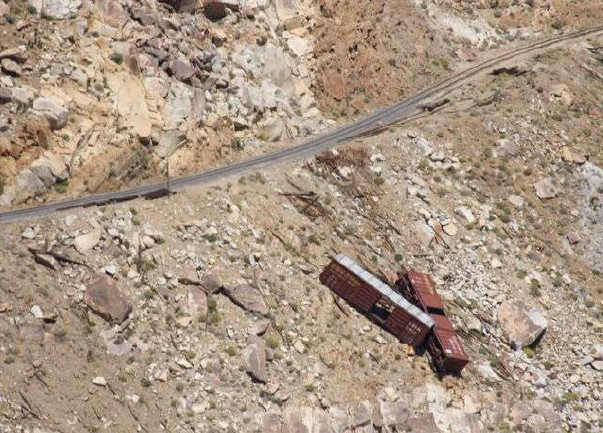
A glorious example of man’s ingenuity and persistence can be found by following the tracks of the San Diego and Arizona Eastern Railroad as it winds its way high above Carrizo Gorge. John Spreckels, of Spreckels sugar fame, was a San Diego resident who was concerned about San Diego’s development. What he felt was needed was a rail line to connect San Diego to markets in the east without having to route through Los Angeles first.